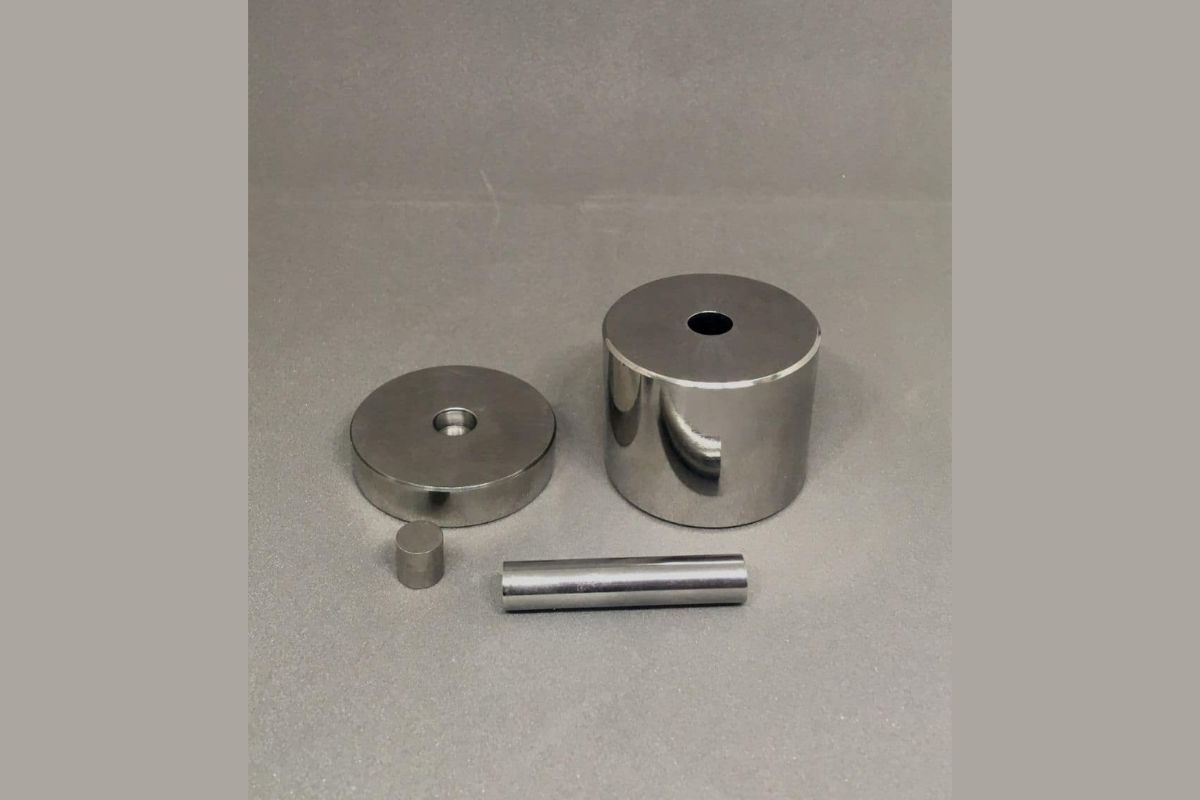
What is the Use of Hydrothermal Reactor?
The hydrothermal reactor is a device that crystallizes substances from high-temperature aqueous solutions at high vapour pressure. The technique is of geologic origin.
It comprises an outer stainless steel jacket and an inner experimental-grade Teflon liner. It can be used for a wide range of synthesis reactions, such as nanomaterials, compound synthesis, material preparation and crystal growth.
Synthesis of Nanoparticles
The synthesis of nanoparticles using a hydrothermal reactor is one of the most efficient ways to produce high-quality and uniform materials. The process involves several complicated phenomena, including hydrodynamics, heat and mass transport, chemical reactions, and particle formation and growth. Therefore, it is important to develop mathematical models incorporating these aspects into a single framework. The results from the modelling will allow for the prediction of particle morphology and size, as well as the reaction conditions needed to achieve the desired results.
A hydrothermal reactor is a sturdy portable reaction chamber that withstands immense pressure and temperature. It is often used in various industrial and R&D applications that require high stability. The reactor can be made of different materials, depending on the type of experiment. For example, some are built to withstand corrosion from acids and alkalis. They also feature an internal Teflon or PPL liner to ensure the safety of the reactants.
Some hydrothermal experiments are conducted in a strong container called an autoclave. These containers are thick-walled steel cylinders with an airtight seal designed to withstand high temperatures and pressures for long periods. Since some solutions are corrosive to steel, special protective inserts are required to prevent the autoclave from being damaged by them. The inserts can fit the interior of the autoclave seamlessly (contact type) or occupy only a part (floating type).
Hydrothermal synthesis is a process in which minerals and metals are grown by heating an aqueous solution to high temperatures and pressures. This method is often used to safely create crystalline phases that cannot be formed at higher temperatures. It was developed by geologists who simulated the conditions during natural mineral formation. This process is often used in the manufacture of oxide ceramics. It can produce pre-dispersed particles with a controlled size distribution, and it is also used to make exotic chemistries, such as mixed metals and doped materials. The disadvantage of this method is that it requires extensive equipment and a large volume of solvent, which makes it difficult to use on a commercial scale.
Synthesis of Metal Alloys
Hydrothermal reactors transform a solution containing different elements into a crystalline powder under controlled conditions in metal alloy synthesis. The reagents are placed in a closed container and heated to the required reaction temperature. The ions of the different metals are attracted to each other by electrostatic forces. These interactions cause the ions to nucleate, grow, and eventually form a crystal. The resulting particles are then separated by centrifugation, and the impurities are deposited on the surface of the crystals. The synthesis is a relatively simple process, and it is suitable for large-scale production.
The advantage of the hydrothermal method is that it can be used with a wide range of metals, is environmentally friendly, and produces highly pure powder materials. However, it requires a high initial investment in equipment and energy. In addition, this method’s synthesis of alloys requires an inert solvent and a high temperature. It is also difficult to control the particle size. A special type of reaction vessel must be used to improve the particles’ stability.
An ideal reactor has a large volume and can accommodate many reactions simultaneously. It has a gas-tight/airtight seal and can be operated at temperatures up to 200°C and pressures up to 3.0MPa. The outer shell of the reactor is made of national standard stainless steel, and the inner lining is experimental grade high-purity PTFE. The reactor lid is a circular tongue-and-groove sealing system with a manual screw.
The Teflon-lined hydrothermal autoclave reactor is widely used in materials, compound synthesis, material preparation, and crystal growth. It is easy to operate and has good mechanical strength. It is available in various sizes and is widely used in university teaching and scientific research units. It is also suitable for use in industrial applications. The Teflon liner protects the stainless steel from corrosion and prevents leakage. It is also resistant to acid and alkali, which makes it a safe and reliable choice for many applications.
Oxidation of Metals
Various metal oxides can be produced using a hydrothermal reaction. This simple and environmentally friendly process produces potentially valuable metal nanoparticles. A new reactor design has been developed that overcomes a fundamental process flaw in previous designs and makes it possible to scale up the production to industrial size. The design is based on the use of supercritical water and has been shown to yield various types of metal oxides with narrow particle size distributions. The key to the new reactor is the patented mixing method, which combines two streams of starting material and supercritical water. This allows the mixture to be stirred rapidly to generate many small particles. The high number of small particles is believed to result in a narrow particle size distribution, which is very important for applications such as solar cells.
The reaction is usually carried out in a PPL (polyphenylene polymer) lined reactor that can be operated at a safe temperature of up to 260 degrees Celsius. The reactor also has a cooling tube and a back pressure regulator. During the oxidation of metals in a continuous hydrothermal reactor, the concentration and the density of the solvent influence the solubility of the oxide particles. It is also important to ensure that the particles are manageable for the desired application.
For example, if the crystal size is too large, the particle will have an irregular shape, which will be difficult to use for applications such as photovoltaic cell manufacturing. Alternatively, if the crystals are too small, they will not have sufficient energy to absorb sunlight, and the cell’s power output will be lower.
The hydrothermal reactor is a closed high-pressure system that simulates the natural processes of mineralization and crystallization. It is used to grow singular crystals, prepare functional ceramic powders, complete organic reactions, and even treat toxic wastes that endanger the environment. It is also useful for preparing and carrying out some metallurgical processes that require elevated temperatures.
Agricultural Chemicals
The hydration of organic molecules is an essential element in the conversion of biomass into useful chemicals. Hydrothermal carbonization (HTC) can be used to transform wet plant biomass into a mixture of industrially useful chemical and energy-yielding products in configurations that recover carbon, detoxify many polluting organic chemicals, and recover elements, including heavy metals, in a closed-loop system.
The HTC process transforms wet organic waste into a solid pellet known as hydrochar by thermal treatment in a pressurized vessel. This product can be converted to fuels such as ethanol but is also usable in the manufacture of chemicals and bio-oil. HTC can process lignocellulosic biomass and other waste materials that are difficult to recycle or degrade, such as sewage sludge or preservative-treated wood waste. HTC is more efficient than other biomass conversion processes, such as anaerobic digestion and Fischer-Tropch synthesis.
Hydrothermal carbonization produces a hydrochar product that contains a mixture of carbon atoms and heteroatoms, notably oxygen, nitrogen and sulphur. These heteroatoms limit bio-crude use in transport applications and can corrode equipment. Removing these heteroatoms by hydrodeoxygenation is a promising technology that can be combined with HTC.
Another potential use for HTC is the production of biomass-based fuels. This is possible because of the low water content of the hydrochar produced in HTC, which makes it more transportable than conventional biofuels. In addition, HTC can produce a renewable fuel that is more economical than petroleum-based gasoline.
The permeability of the hydrochar produced in HTC is comparable to that of petroleum-based crude oil, making it an attractive feedstock for transport fuels. However, the process must be improved and scaled up to reduce costs. Moreover, the hydrochars generated by HTC are likely to contain large amounts of contaminants, such as nitrogen and sulphur, which can damage the environment. These contaminates are also likely to decrease the energy density of the bio-crude. This problem can be solved by modifying the reactor design or using other technologies, such as membrane distillation.