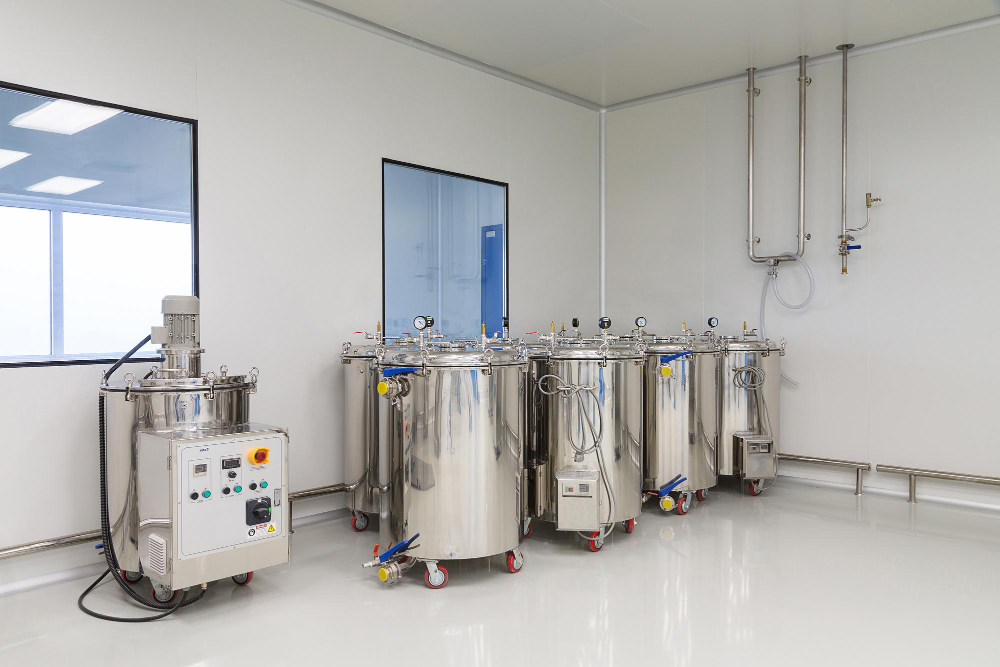
The Role of Advanced Technology in Modern Fermenter Manufacturing
Introduction:
Fermenters are indispensable tools in a wide range of industries, from pharmaceuticals and biotechnology to food and beverage production. These vessels serve as controlled environments where microorganisms thrive, enabling the production of essential products like antibiotics, enzymes, beer, and yogurt. In recent years, the integration of advanced technology has fundamentally transformed fermenter manufacturing, ushering in a new era of efficiency, higher yields, and superior product quality. This article delves deeper into the pivotal role advanced technology plays in modern fermenter manufacturing.
1. Automation and Control Systems:
Advanced technology has revolutionized fermenter manufacturing by introducing sophisticated automation and control systems. These systems offer precise monitoring and regulation of critical parameters such as temperature, pH, oxygen levels, and agitation speed. Consequently, a fermenter manufacturer can maintain optimal conditions for microbial growth and product formation, leading to improved yields and reduced batch-to-batch variations.
Automation not only enhances efficiency but also ensures consistency in the fermentation process. Human error is minimized, and the risk of deviations that can compromise product quality is significantly reduced. Furthermore, these systems often incorporate fail-safe mechanisms, providing an additional layer of security and reliability.
2. Bioprocess Sensors:
The integration of bioprocess sensors is a cornerstone of modern fermenter technology. These sensors provide real-time data on vital process parameters, allowing operators to make informed decisions promptly. pH sensors, dissolved oxygen sensors, and biomass sensors are just a few examples of the sensors utilized in fermenter manufacturing. They ensure that the fermentation process remains within the desired range, mitigating the risk of contamination and product loss.
Bioprocess sensors are critical for maintaining the health of the microbial culture within the fermenter. By continuously monitoring parameters like pH and oxygen levels, manufacturers can optimize conditions for microbial growth and product formation. This precision results in higher yields and more consistent product quality.
3. Computational Modelling:
The advent of computational modelling and simulation has had a profound impact on fermenter manufacturing. Advanced software tools enable engineers and scientists to predict and optimize fermentation processes before they even commence. This not only saves time and resources but also ensures that the final product consistently meets quality standards. Computational modeling aids in the design of fermenter systems tailored to specific production requirements.
Simulation software allows manufacturers to explore various scenarios, experiment with different process parameters, and identify potential bottlenecks or challenges. This proactive approach minimizes the risks associated with scaling up production or introducing new products. Ultimately, computational modeling accelerates the development and optimization of fermentation processes.
4. Materials and Design:
Advanced materials and design principles have significantly improved the durability and efficiency of fermenters. Materials like stainless steel and specialized coatings are corrosion-resistant and easy to clean, ensuring product purity and reducing maintenance costs. These materials are also highly compatible with the stringent hygiene standards required in industries such as pharmaceuticals and biotechnology.
Innovative designs have enhanced the performance of fermenters. Bioreactor geometries and impeller configurations have been optimized to maximize mixing efficiency while minimizing energy consumption. This not only saves energy but also ensures that microbial cultures are adequately mixed, promoting uniform growth and product formation.
5. Process Monitoring and Data Analytics:
Modern fermenters are equipped with advanced data acquisition and analytics capabilities. This enables the continuous monitoring of fermentation processes, helping operators detect deviations and take corrective actions in real time. Additionally, the collected data can be analyzed to identify trends and patterns, leading to process optimization and improved product quality.
Data analytics can uncover hidden insights in fermentation processes. By analyzing historical data, manufacturers can identify areas for improvement, fine-tune their processes, and optimize resource utilization. This data-driven approach enhances efficiency, reduces waste, and ultimately contributes to cost savings.
6. Quality Assurance and Regulatory Compliance:
The integration of advanced technology in fermenter manufacturing plays a pivotal role in meeting stringent quality assurance and regulatory requirements. Fermenter systems can now be equipped with built-in validation and compliance features, ensuring that processes adhere to industry standards and guidelines.
Compliance with regulatory requirements is crucial, especially in industries such as pharmaceuticals and biotechnology, where product safety and efficacy are paramount. Advanced technology provides the tools necessary to automate documentation, track changes, and maintain comprehensive records, simplifying the auditing and validation processes.
7. Scalability:
Scalability is a key consideration in fermenter manufacturing, and advanced technology has simplified the process of transitioning from laboratory-scale to industrial-scale production. Manufacturers can replicate successful lab-scale processes on a larger industrial scale with greater ease and precision.
Advanced technology allows for the seamless scaling up or down of fermentation processes. Manufacturers can confidently expand their production capacity when needed, knowing that the technology in place is adaptable and reliable. This flexibility enables businesses to respond to changing market demands more effectively.
Conclusion:
The role of advanced technology in modern fermenter manufacturing is transformative, offering enhanced efficiency, superior product quality, and increased production yields. As technology continues to advance, we can anticipate even more innovations that will further revolutionize the way fermenters are designed and utilized across various industries. Embracing these technological advancements is not just an option but a necessity for businesses looking to stay competitive in today’s rapidly evolving market. Fermenter manufacturing has entered a new era driven by innovation, automation, and data-driven decision-making, enabling industries to harness the full potential of fermentation processes.