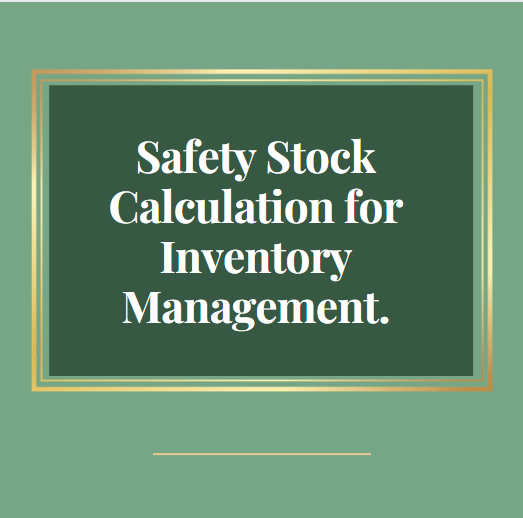
Mastering Safety Stock Calculation for Optimal Warehouse Inventory Management.
Introduction
In the intricate dance of warehouse inventory management, one crucial partner is often overlooked: safety stock. This unsung hero acts as a buffer, ensuring that your operations continue to flow smoothly even in the face of unexpected demand spikes or supply chain hiccups. In this comprehensive guide, we’ll delve into the nitty-gritty of safety stock calculation, equipping you with the knowledge to fine-tune your warehouse inventory management strategy.
Understanding Safety Stock: A Shield Against Uncertainty.
In warehouse inventory management, safety stock is the extra inventory maintained to mitigate the risk of stockouts. It acts as a safety net, offering a cushion against unexpected fluctuations in demand or delays in the supply chain. Striking the right balance is key – too much safety stock ties up capital, while too little can lead to stockouts and dissatisfied customers.
Factors Influencing Safety Stock Levels
- Demand Variability: The more unpredictable your demand, the higher your safety stock should be. Seasonal products, trendy items, and new product launches often exhibit higher demand variability.
- Lead Time Variability: Longer and more variable lead times necessitate higher safety stock levels. This accounts for potential delays in receiving replenishment orders.
- Service Level Targets: The desired level of customer service plays a pivotal role in safety stock calculation. A higher service level target requires more safety stock to meet customer demands consistently.
Safety Stock Calculation Methods
- Basic Safety Stock Formula
The basic safety stock formula considers average demand, lead time, and standard deviation in demand:
�����������=(�∗��)∗��SafetyStock=(Z∗σd)∗LT
Where:
- �Z represents the Z-score associated with the desired service level.
- ��σd is the standard deviation of demand during lead time.
- ��LT stands for lead time in days.
Periodic Review System
Safety stock is determined at fixed review intervals in a periodic review system. This method is suitable for products with predictable demand patterns.
Continuous Review System
In a continuous review system, safety stock is constantly monitored and adjusted based on real-time data. This approach is more adaptable to products with erratic demand.
Optimizing Safety Stock Levels
ABC Analysis
Classify your products (A, B, and C) based on their contribution to revenue. Allocate more safety stock to high-value ‘A’ items and less to ‘C’ items.
Collaborative Planning, Forecasting, and Replenishment (CPFR)
Engage in collaborative planning with suppliers to enhance forecast accuracy and reduce the need for excess safety stock.
Demand Forecasting
Leverage advanced forecasting techniques and software to predict future demand better, allowing for more accurate safety stock calculations.
Utilize Inventory Management Software
Invest in cutting-edge warehouse inventory management software that integrates safety stock optimization algorithms to automate and fine-tune your inventory levels.
Conclusion
In the dynamic world of warehouse inventory management, safety stock emerges as a linchpin, ensuring operational continuity in the face of uncertainties. By employing advanced safety stock calculation methods and leveraging modern technologies, businesses can strike the perfect balance between customer satisfaction and capital efficiency. Remember, safety stock is your most graceful dancer in the complex ballet of supply chains, elegantly gliding you through unpredictable demand surges and supply chain disruptions. Embrace it, and watch your warehouse operations flourish.