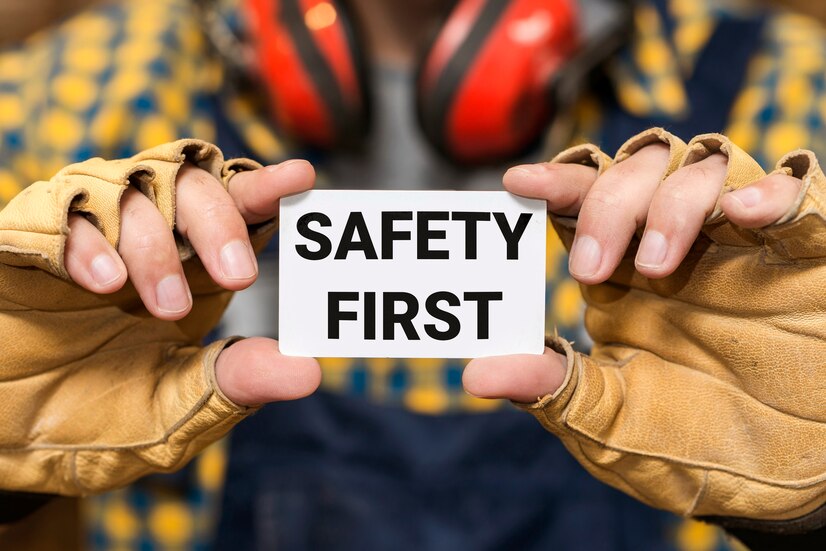
Common Mistakes to Avoid When Creating a Safety Case
In industries such as aviation, healthcare, automotive, and nuclear power, ensuring safety is paramount. Safety cases play a critical role in demonstrating that safety measures are in place and that systems and processes are designed to prevent accidents and protect people and the environment. However, creating an effective Safety Case can be a complex and challenging task, and there are common mistakes that organizations must avoid. In this article, we will explore some of these pitfalls and discuss how to steer clear of them.
Lack of Clarity and Structure
One of the most common mistakes in safety case creation is the lack of clarity and structure. Safety cases should be well-organized, easy to understand, and provide a clear and concise argument for the safety of a system or process. Avoid including too much technical jargon or irrelevant information that can confuse stakeholders. A well-structured safety case should follow a logical flow, presenting the Fire And Explosion Analysis, risk assessment, safety measures, and safety management plan in a coherent and organized manner.
Ignoring Stakeholder Involvement
Another mistake is failing to involve all relevant stakeholders in the safety case development process. Safety cases often require input from various departments and personnel, including engineers, operators, maintenance teams, and safety experts. Neglecting their perspectives can lead to critical oversights. Collaborative efforts can help identify potential risks and develop effective mitigation strategies that might otherwise be missed.
Overlooking Human Factors
Human error is a significant contributor to safety incidents in many industries. Neglecting human factors in safety cases is a common mistake. Safety cases should consider the impact of human actions and errors, as well as factors like fatigue, workload, and training. Incorporating human factors analysis can help design systems that are more resilient to human error and minimize the potential for accidents.
Underestimating the Importance of Documentation
Comprehensive documentation is vital in safety case development. Failing to maintain accurate and up-to-date records of all safety-related activities is a serious mistake. Organizations must document hazard identification, risk assessments, safety measures, safety audits, and safety management procedures. Proper documentation not only ensures transparency but also helps in tracking the evolution of safety measures and the effectiveness of safety management over time.
Inadequate Risk Assessment
One of the primary objectives of a safety case is to identify and assess potential risks. Inadequate risk assessment is a common mistake that can lead to the underestimation of risks or the failure to consider all relevant hazards. Organizations should use a systematic and well-established method for risk assessment, considering not only the likelihood and consequences of accidents but also the potential consequences to the environment and society.
Neglecting Change Management
Over time, systems and processes undergo changes, whether due to technology upgrades, personnel shifts, or modifications to procedures. Neglecting change management in safety cases is a significant error. Organizations must have robust processes for managing changes and ensuring that safety measures are updated accordingly. Failure to address change management can lead to outdated safety cases that no longer reflect the actual safety status of a system or process.
Lack of Testing and Validation
Safety cases should not be based solely on theoretical assessments. Another mistake is the lack of actual testing and validation to support safety claims. Real-world testing and validation are crucial to demonstrate that safety measures work as intended. They provide tangible evidence that a system or process is safe and can help identify potential flaws or limitations that may not be apparent through theoretical analysis alone.
Underestimating the Importance of Continuous Improvement
A safety case is not a static document but should be a living, evolving document. Failing to recognize the importance of continuous improvement is a common mistake. Organizations must regularly review and update their safety cases to reflect changes in technology, regulations, and organizational practices. Continuous improvement ensures that safety measures remain effective and relevant over time.
Complacency is another critical mistake to avoid. Overconfidence in safety measures can lead to a false sense of security. Organizations should always be open to evaluating their safety practices and considering the possibility of new and unforeseen risks. Safety cases should not only focus on what is known but also on what could potentially go wrong.
Conclusion
Creating a safety case is a vital step in ensuring the safety of complex systems and processes, but it can be a challenging task. Organizations must be mindful of the common mistakes discussed in this article, as they can undermine the effectiveness of a safety case and compromise the safety of people and the environment. By avoiding these pitfalls and focusing on clarity, stakeholder involvement, human factors, documentation, risk assessment, change management, testing, continuous improvement, and maintaining a realistic view of safety, organizations can develop robust and reliable safety cases that stand up to scrutiny and help prevent accidents and disasters.